Creating Informative Content for B2B Stone Polishing Customers
When it comes to selling stone polishing products or services in the B2B sector, the key to standing out is not just about showcasing the latest technology or the most competitive prices. It’s about offering content that adds value, educates, and addresses the specific challenges your customers face. Stone polishing, an essential part of maintaining the beauty and durability of stone surfaces, involves a range of products and techniques that many businesses may not be fully familiar with. By creating informative content, you can establish your brand as a trusted partner and a valuable resource in the stone polishing industry.
The goal of informative content is to offer your customers not just a product, but a deeper understanding of how to solve their unique challenges. Whether you’re catering to contractors, architects, or business owners in industries like construction, interior design, or property management, your content should serve to solve problems and provide insights that help them make better, more informed decisions.
Understanding your audience is the first step in crafting content that resonates. In the B2B world, clients are looking for practical solutions, not fluff. They want to know how your stone polishing products or services can improve their workflow, reduce costs, or enhance the quality of their work. This is why it’s crucial to dive deep into their pain points. For example, contractors might be struggling with time-consuming polishing jobs or inconsistency in results. By addressing these issues in your content, you can show them how your offerings will improve their processes.
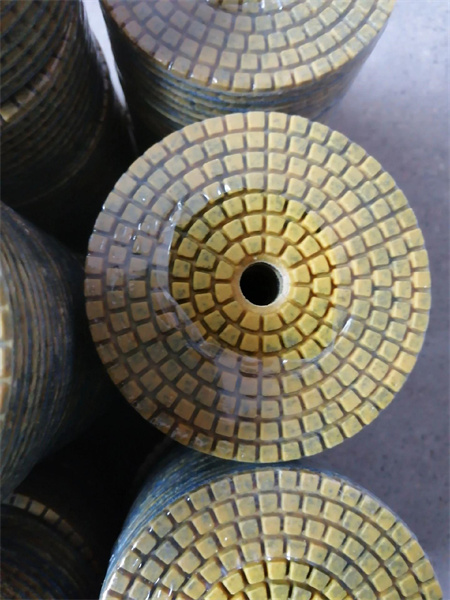
Beyond case studies, how-to guides and educational blog posts can play a significant role in building your authority in the stone polishing industry. Many B2B customers are looking for ways to streamline their operations or improve their knowledge of materials and techniques. Offering in-depth guides on topics like “The Best Techniques for Polishing Marble Floors” or “How to Choose the Right Polishing Tools for Granite” will attract potential customers who are looking to improve their business practices. The more you help them, the more likely they are to trust you when they’re ready to make a purchase.
Video content is another powerful tool to engage your audience. Demonstrating how your products work, or offering tutorials on proper polishing techniques, can bridge the gap between theory and practice. Videos allow you to show real-time results, giving potential customers a more dynamic and engaging way to learn about your offerings. For example, a time-lapse video of a polishing job from start to finish can highlight the precision and effectiveness of your tools, making it easier for customers to visualize how they can use them in their own operations.
At the same time, don’t overlook the power of social proof. Customer testimonials, online reviews, and expert endorsements all contribute to building trust and credibility. When your customers see that others in the industry are successfully using your products, they’re more likely to consider your brand. Including customer feedback on your website or in your marketing materials can help reassure prospects that they’re making the right choice by partnering with you.
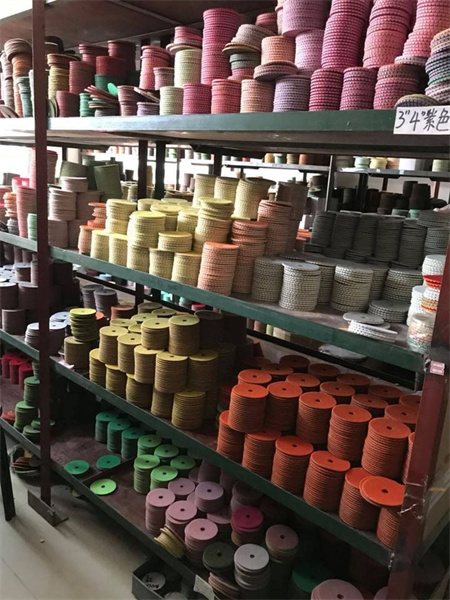
In conclusion, creating informative content for B2B stone polishing customers isn’t just about selling your products; it’s about building a relationship and becoming a trusted resource. By understanding your audience’s challenges, offering practical advice, and providing real-world examples, you position your brand as more than just a vendor—you become a valuable partner in their success. Whether through case studies, how-to guides, or video demonstrations, your content should reflect the expertise and reliability that your customers seek. And by staying current with industry trends, you ensure that your content remains relevant, helping to attract and retain loyal B2B clients.
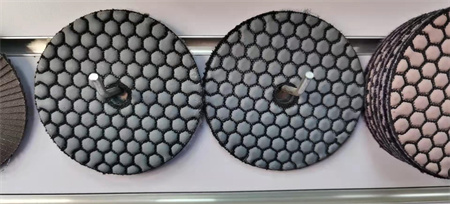