How Diamond Hardness Affects Polishing Performance
When it comes to diamonds, their unparalleled beauty and strength make them a symbol of luxury and precision. But beyond their sparkling allure, diamonds are prized for a crucial characteristic that influences a variety of applications—hardness. The hardness of a diamond plays an integral role in its performance, particularly in the context of polishing. Understanding how diamond hardness affects the polishing process is essential, whether you’re working in a jewelry shop, an industrial setting, or even in scientific research.
Diamonds, being the hardest known natural material on Earth, possess a hardness rating of 10 on the Mohs scale. This exceptional hardness is a major factor in their use for cutting, grinding, and polishing other materials. However, not all diamonds are created equal in terms of hardness. Natural diamonds, synthetic diamonds, and different diamond grades can vary in their hardness levels, which in turn, directly impacts their polishing performance.
A diamond’s hardness influences its ability to maintain its edge and shape during the polishing process. When diamonds are used as abrasives, their hardness allows them to effectively scratch, grind, or polish even the toughest surfaces. The harder the diamond, the more resistant it is to wear and degradation during use. This means that diamonds with higher hardness will continue to perform efficiently over a longer period of time, reducing the need for frequent replacement or reconditioning of the polishing tools.
But how does this translate to the polishing results we see? Polishing is a delicate balance of abrasion and finesse, where the goal is not only to smooth the surface but to achieve a mirror-like finish. The hardness of the diamond abrasives directly affects how smooth and even the finish will be. Softer abrasives, or those with lower hardness, may not have the staying power to maintain a consistent, smooth surface. Instead, they may cause uneven polishing or leave behind micro scratches that compromise the finish quality. On the other hand, diamonds with high hardness tend to leave an extremely fine finish because they maintain their cutting ability and don’t break down as quickly.
The influence of diamond hardness is especially noticeable in industrial diamond polishing, where diamonds are used to finish surfaces of metals, ceramics, and glass. In these applications, the performance of the polishing tool can make all the difference. Harder diamonds are capable of achieving more precise and fine results, while softer diamonds may leave visible imperfections or require longer processing times. Furthermore, diamonds used in these industries often come in the form of powders or bonded abrasives, where the grade and size of the diamonds can further influence the polishing speed and quality.
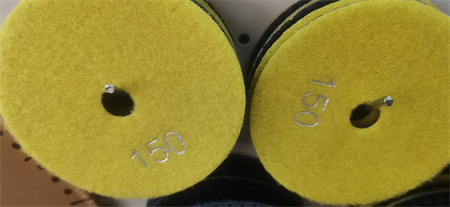
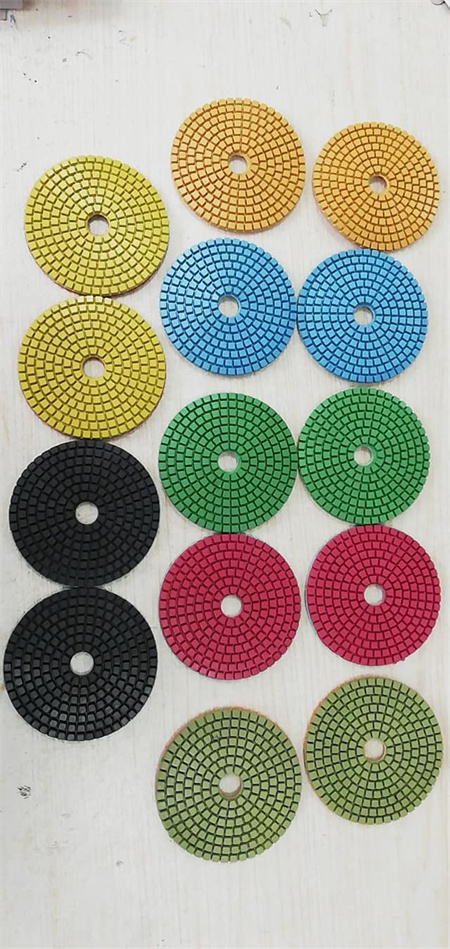
In jewelry, for instance, the quality of the diamond’s cut and polish is a reflection of both the initial hardness and how well it was worked with during the polishing process. A diamond with a higher hardness can hold a fine polish for much longer, which is why diamonds with the best quality cuts often appear to have more brilliant and sharper reflections.
The polishing performance also hinges on the overall condition of the polishing tool. If a diamond loses its sharpness or begins to wear down, it may start leaving behind scratches or fail to provide the desired finish. The longevity of the polishing tool itself is a key consideration, which is why harder diamonds tend to be favored in settings where precision and consistency are crucial.
In conclusion, while hardness is just one factor in the complex world of diamond polishing, it undeniably plays a pivotal role in determining the final outcome. A diamond’s ability to maintain its edge and resist wear directly influences its polishing effectiveness, impacting everything from industrial applications to the fine craftsmanship seen in diamond jewelry. Understanding the relationship between hardness and polishing performance helps ensure that the right diamond is chosen for the right job, resulting in a polished surface that’s not just smooth, but flawless.
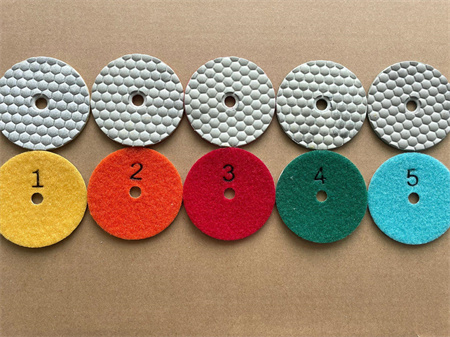