How Thickness Impacts Polishing Pad Performance
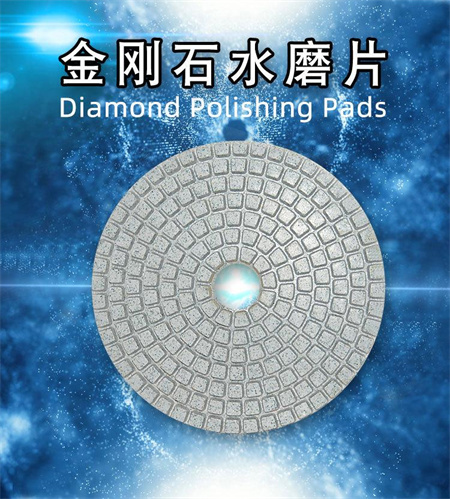
To begin with, thickness has a direct effect on the pressure distribution during polishing. A thicker pad allows for more even pressure across the surface being worked on. This means the pad has the ability to conform to irregularities on the surface, ensuring a more uniform finish. Conversely, thinner pads may apply pressure in a less even manner, potentially leading to streaks, swirl marks, or uneven polishing. When working on delicate or intricate surfaces, a thicker pad is often the safer choice as it can provide better control and a more consistent application of compound or polish.
Another critical aspect influenced by pad thickness is heat dissipation. Polishing generates heat, and how well a pad handles this heat can make a significant difference in its performance and longevity. Thicker pads tend to absorb and distribute heat more effectively, preventing the surface from overheating. This is particularly important when working with heat-sensitive materials or paints, as excessive heat can cause the surface to burn or distort. Thinner pads, on the other hand, may not offer the same level of heat management, leading to overheating and potentially damaging the workpiece.
In addition, pad thickness plays a role in the amount of product used during the polishing process. Thicker pads tend to hold more compound or polish, allowing for a more consistent application throughout the job. This can be especially advantageous when working on large surfaces or during extended polishing sessions. The added thickness helps retain the product, minimizing the need for frequent reapplication. However, a pad that is too thick can sometimes lead to product waste if it holds too much, which might not be ideal for smaller or more intricate tasks.
Thicker pads also excel in handling more aggressive polishing jobs. When working on surfaces that require a more aggressive approach, such as heavily oxidized or scratched paint, a thicker pad can absorb the additional pressure and force needed to remove imperfections. It allows for better cutting power without risking surface damage. On the flip side, thinner pads are generally more suitable for lighter polishing tasks, like finishing work or buffing out minor imperfections. While thinner pads can still deliver excellent results, their cutting power is limited compared to thicker counterparts.
However, there are trade-offs when using thicker pads. One of the main considerations is that thicker pads tend to be slower when it comes to polishing large, flat surfaces. This is because they typically require more time to cover the same area compared to thinner pads. While they may provide better results in terms of quality and consistency, they may not be the most efficient choice for high-speed jobs that require a faster turnover. Thin pads, on the other hand, excel in speed but may compromise on the depth of cut and finish quality.
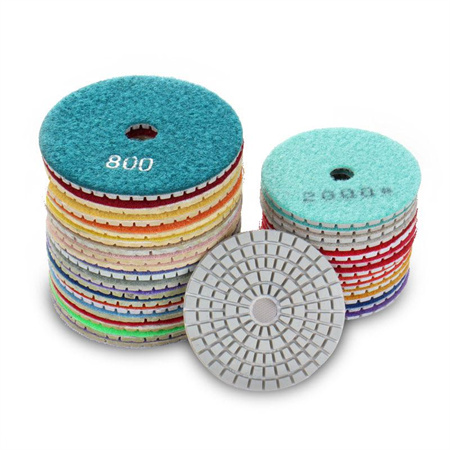
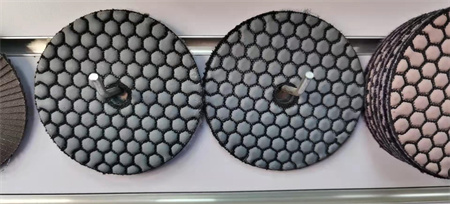
Ultimately, understanding the impact of pad thickness on polishing performance is key to optimizing your results. Thicker pads provide more control, better heat dissipation, and enhanced product retention, making them ideal for certain tasks, while thinner pads offer speed and precision for lighter work. Finding the right balance based on the specific needs of your project will ensure that you achieve the best possible finish, without compromising on quality or efficiency. Whether you are restoring a vintage car’s paint or simply giving your countertops a shine, the right polishing pad thickness will help you achieve the results you’re looking for.