How Grit Density Influences Polishing Pad Efficiency
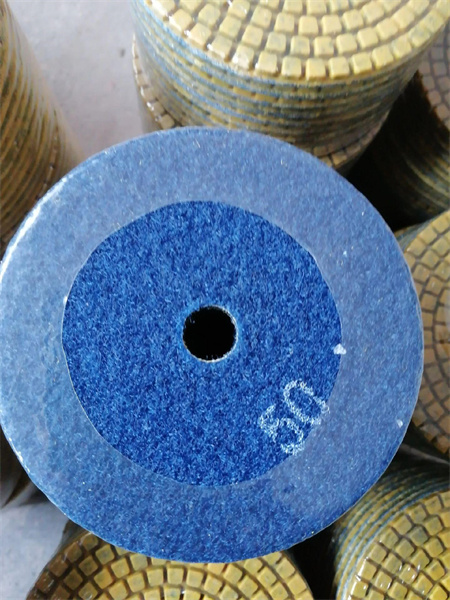
To understand how grit density affects polishing pad performance, it’s essential to first consider what grit density actually means. Simply put, grit density refers to how closely the abrasive particles are arranged on the surface of the pad. A pad with higher grit density will have more abrasive particles per unit of surface area, while a lower grit density pad will feature fewer abrasives spaced further apart. This difference in structure directly affects how the pad interacts with the material being polished, as well as the overall outcome of the polishing process.
One of the most noticeable effects of grit density on polishing pad efficiency is the rate at which material is removed. High-density pads, due to the sheer number of abrasive particles, tend to cut faster, which makes them ideal for heavy-duty applications where speed is crucial. Whether you’re polishing concrete floors, automotive paint, or marble countertops, a high-density pad will remove material more aggressively. This can be especially beneficial when you’re working with hard surfaces or materials that require a significant amount of abrasion to reach a smooth finish.

Another key factor affected by grit density is the lifespan of the polishing pad. Pads with higher grit density tend to wear down more quickly because the abrasives are more tightly packed, leading to faster deterioration under heavy use. However, for high-intensity polishing tasks, this might be a necessary trade-off. Low-density pads, on the other hand, last longer since the abrasives are spaced farther apart, reducing wear and tear over time. This makes them more suitable for lighter, routine polishing tasks where longevity is more important than speed.
The ability of a polishing pad to maintain consistency in its performance throughout the process is also tied to its grit density. High-density pads offer consistent abrasion, but as they wear down, their efficiency can decrease more rapidly compared to their lower-density counterparts. As the abrasives become flattened or embedded with material, the pad’s cutting action might diminish. Low-density pads, however, maintain their overall effectiveness for a longer period, as they are less prone to the rapid flattening of abrasives.
Grit density also influences heat generation during the polishing process. High-density pads, because they pack more abrasives into the same area, tend to generate more heat. This is particularly true when polishing at higher speeds or applying more pressure. Excessive heat can cause the polishing pad to degrade faster, leading to a decrease in its overall lifespan and efficiency. Lower-density pads, in contrast, distribute the heat more evenly, which can help maintain the integrity of both the pad and the surface being polished.
It’s important to remember that grit density alone isn’t the sole determinant of polishing pad efficiency. Factors such as the type of abrasive material, the flexibility of the pad, and the specific machine settings all play a role in determining how effective the pad will be. However, understanding the influence of grit density can help you select the right pad for your specific needs, whether you’re aiming for a fast, aggressive cut or a slow, detailed finish.
In summary, grit density is a crucial factor that influences the efficiency of polishing pads. Whether you’re looking for speed, precision, durability, or heat control, the grit density of your polishing pad plays a pivotal role in achieving the desired outcome. By understanding how this variable affects the polishing process, you can make more informed decisions, ensuring that your tools are best suited for the job at hand.
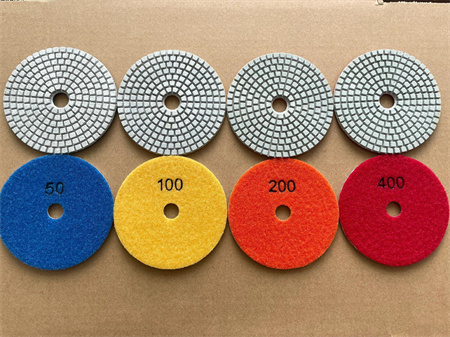