Polishing Uneven Surfaces with Flexible Diamond Pads
When it comes to achieving a smooth, flawless finish on a variety of surfaces, particularly those that are uneven or irregular, flexible diamond pads have emerged as a game-changer in the world of surface polishing. These versatile tools offer an effective solution for polishing everything from concrete to stone, marble, and even glass. But what exactly makes flexible diamond pads so effective, and how do they handle the challenge of uneven surfaces? Let’s dive into the specifics of this incredible tool and explore how it can revolutionize your polishing process.
Uneven surfaces are notorious for posing challenges to anyone trying to achieve a polished, refined look. Whether it’s the natural undulations of stone, the imperfections in concrete, or the subtle irregularities in tiles, these surfaces can frustrate even the most experienced craftsmen. Traditional polishing tools often struggle with these variations, especially when consistency and precision are crucial. However, flexible diamond pads have proven to be one of the most effective solutions for polishing such surfaces with ease and accuracy.
One of the standout features of flexible diamond pads is their ability to conform to the contours of uneven surfaces. Unlike rigid grinding tools that can leave behind marks or miss certain areas altogether, these pads are designed to bend and flex with the shape of the surface. This flexibility allows for a more even application of pressure, ensuring that every nook and cranny is polished uniformly. Whether the surface is concave, convex, or simply irregular, the flexible diamond pad molds itself to the shape, providing a smooth and consistent finish throughout the process.
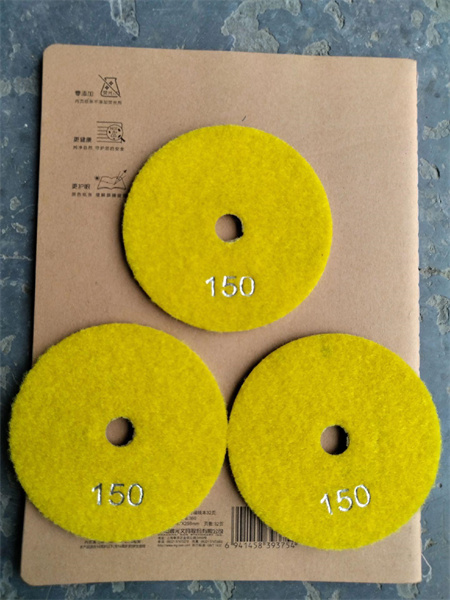
Another benefit of flexible diamond pads is their versatility. They come in various grits, ranging from coarse to fine, allowing users to select the perfect pad for the job at hand. Whether you need to smooth out rough surfaces or polish them to a mirror-like finish, there is a flexible diamond pad suited for the task. This range of grit sizes makes it possible to use these pads across different stages of the polishing process, ensuring optimal results from start to finish.
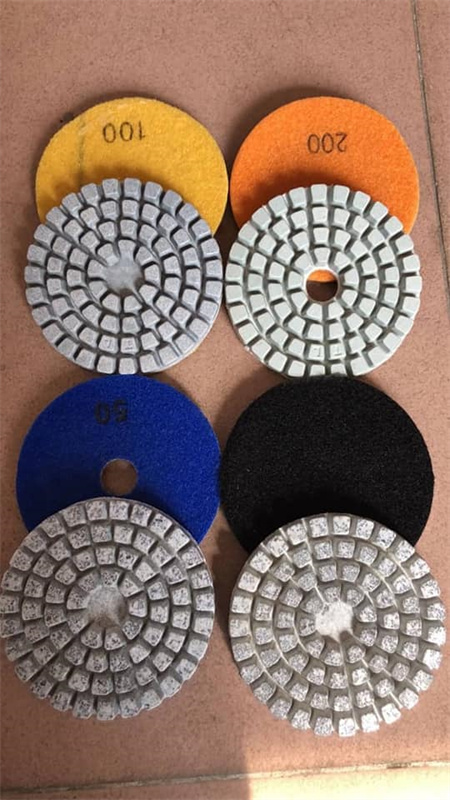
Moreover, flexible diamond pads are easy to use, making them accessible for both professionals and DIY enthusiasts. Their user-friendly design means that even those with little experience in surface polishing can still achieve high-quality results. The pads can be attached to a variety of polishing machines, from handheld units to larger, more industrial-grade tools, adding another layer of convenience and flexibility to the process.
Durability is another key advantage that flexible diamond pads bring to the table. Unlike traditional abrasives that wear down quickly, diamond pads retain their cutting power over time. This not only makes them more cost-efficient but also ensures that users can rely on them for consistent performance throughout the polishing process. Whether you’re working on a large commercial project or a smaller, more intricate task, these pads will continue to deliver exceptional results without the need for constant replacements.
Despite their strength and durability, flexible diamond pads are also relatively gentle on the surfaces they work on. They don’t generate excessive heat, which can cause warping or other forms of damage to delicate surfaces. This makes them ideal for polishing a wide range of materials, from softer stones to more sensitive finishes like glass or ceramic.
In summary, polishing uneven surfaces with flexible diamond pads is an incredibly efficient, cost-effective, and versatile approach. Whether you’re looking to achieve a professional-level finish on concrete floors or bring out the natural beauty of marble countertops, these pads offer a solution that adapts to the task at hand. Their ability to conform to irregular surfaces, their longevity, and their precision make them an indispensable tool for anyone involved in surface polishing. So, if you’re ready to take your polishing projects to the next level, flexible diamond pads are the tool you’ve been waiting for.
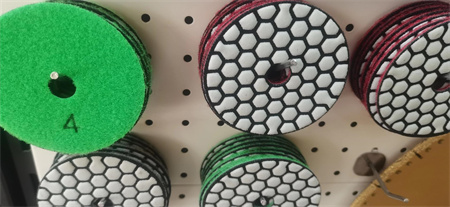