Creating a Competitive Advantage with Custom Diamond Pads
In today’s fast-paced manufacturing and industrial environments, gaining a competitive edge means constantly innovating and finding solutions that increase efficiency, reduce costs, and enhance performance. For many businesses, one such solution lies in custom diamond pads. These specialized tools are not just about polishing or grinding—they can be the key to unlocking new levels of precision, durability, and productivity.
Diamond pads, known for their durability and effectiveness in abrasive tasks, are essential in a variety of industries, from semiconductor manufacturing to automotive and aerospace. When these pads are custom-designed to meet the specific needs of a given application, they can offer even more significant benefits. A custom solution allows for better performance, cost efficiency, and the ability to meet unique challenges that off-the-shelf products simply cannot address.
One of the most significant advantages of custom diamond pads is the ability to tailor the abrasive qualities to the task at hand. Every material has its own unique set of requirements when it comes to finishing or smoothing, and standard pads are often too generic to meet those needs effectively. By working with a supplier that can provide bespoke solutions, businesses gain the ability to fine-tune the pad’s grit, thickness, shape, and even the diamond concentration. This level of customization leads to more efficient processes, less waste, and improved outcomes, which in turn increases overall productivity and reduces production costs.
Customization also means that businesses can adapt to changes in the manufacturing environment. Whether it’s handling a new material or needing to speed up a particular process, a custom diamond pad can be designed to adjust to these changes. For example, if a company switches to a more delicate material that requires a finer polish or a faster cycle time, a tailored pad can help maintain consistency and precision without having to overhaul entire workflows. This flexibility allows manufacturers to stay ahead of the curve, quickly adapting to market demands and staying competitive.
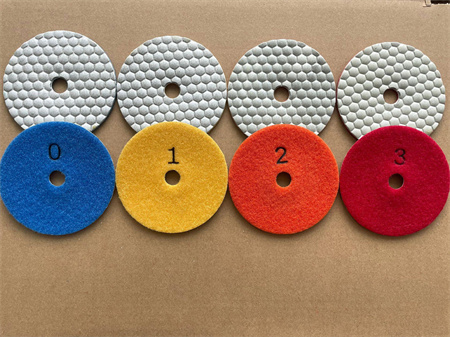
Beyond improving operational efficiency, custom diamond pads can also enhance product quality. For manufacturers focused on high-end products or those in highly regulated industries, the precision and consistency that a custom-designed pad offers are invaluable. By ensuring that each component or surface is finished to the exact specifications, these pads can help maintain the highest standards of quality control. In industries like aerospace or medical device manufacturing, even the smallest deviation in surface finish can have costly and dangerous consequences. Custom pads give businesses the confidence that their products will meet rigorous standards time after time.
The environmental impact is another consideration that is often overlooked but can play a crucial role in competitive advantage. By choosing custom diamond pads, businesses can minimize waste. Standard pads are typically designed to cover a broad range of applications, meaning that they may not be the most efficient or sustainable choice for a specific task. Custom pads, however, are designed with the precise material, size, and shape in mind, which helps reduce excess material and unnecessary abrasion, ultimately leading to less waste and a smaller carbon footprint.
Customer service and support are vital aspects of working with a supplier of custom diamond pads. Unlike generic pads, where the relationship often ends once the product is purchased, a custom solution requires close collaboration between the supplier and the manufacturer. This ongoing partnership ensures that the pads continue to perform at optimal levels and allows for adjustments or improvements as needs change. With a supplier who is willing to work hand-in-hand with your business, you gain a trusted ally who understands your unique challenges and is committed to helping you succeed.
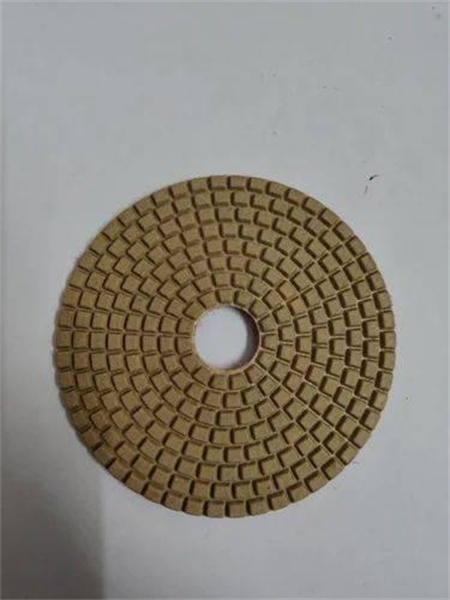
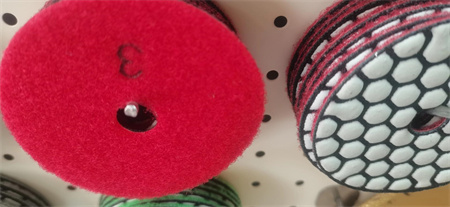