Diamond polishing pads, often used in the surface treatment of stone, concrete, and other hard materials, are an essential tool in achieving a smooth and glossy finish. Whether designed for wet or dry polishing, these pads are engineered to handle the rigorous demands of various applications. The manufacturing process of diamond polishing pads involves a combination of advanced technology and precision, ensuring high performance for both commercial and industrial users worldwide.
The creation of diamond polishing pads begins with the selection of high-quality materials. The core of the pad consists of synthetic rubber or resin, which provides durability and flexibility. Embedded in the resin are industrial-grade diamonds, known for their hardness and efficiency in grinding and polishing. These diamonds are carefully arranged and bonded to the pad using a specialized process that ensures even distribution, providing uniform abrasion during use.
For wet polishing pads, water is used to cool down the surface and remove debris during the polishing process. This helps maintain the quality of the finish by reducing heat buildup and preventing surface discoloration. The wet pads are designed with a higher level of flexibility and softness, which allows them to conform to the shape of the material being polished, making them ideal for softer stones or more intricate workpieces.
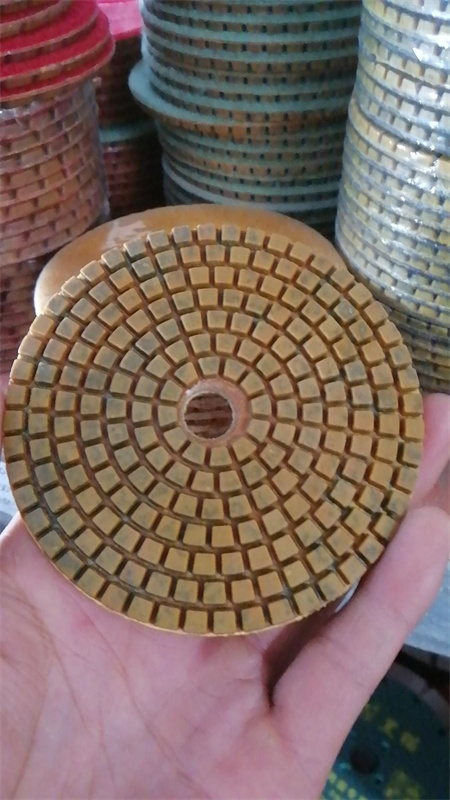
Throughout the manufacturing process, quality control plays a crucial role in ensuring that each diamond polishing pad meets the highest standards. The pads are rigorously tested for durability, performance, and consistency. Once they pass these tests, they are packaged and prepared for global distribution. The pads are available in various grits, allowing users to choose the perfect tool for their specific needs, whether they are achieving a rough grind or a fine, polished surface.
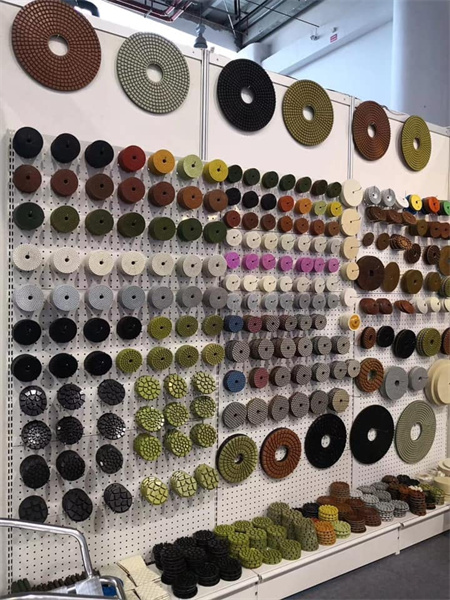
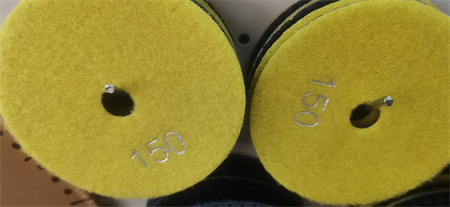