Increasing Efficiency in Polishing Work with Advanced Pads
Polishing has always been a critical part of many industries, from automotive detailing to manufacturing and restoration projects. Over the years, the tools and materials used for polishing have evolved significantly, but one of the most remarkable advancements in this field has been the development of advanced polishing pads. These innovative pads are transforming the way professionals approach their work, increasing both efficiency and quality.
Advanced polishing pads are not just a simple replacement for traditional ones; they represent a leap forward in technology and design. One of the key features that set these pads apart is the materials used in their construction. Modern pads are crafted from a variety of high-tech compounds, designed to enhance their performance on different surfaces. For instance, some pads are made from microfiber, which is highly effective at trapping dust and debris, ensuring a smoother, more consistent finish. Others are composed of advanced polymers that provide better durability, making them suitable for high-intensity use in industrial environments.
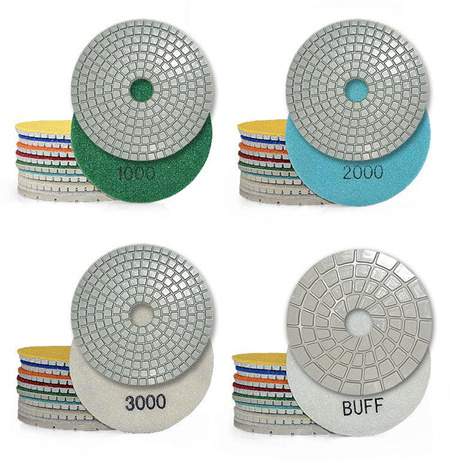
Another major benefit of advanced polishing pads is their versatility. Depending on the job at hand, different pads can be used to achieve a range of finishes. Whether it’s a high-gloss, mirror-like shine or a more subdued, satin finish, these pads are designed to cater to different levels of intensity and polishing needs. The variety in texture, from soft and plush to more firm and aggressive, allows users to select the right pad for the right job, ensuring that they can tackle a wide range of materials, from delicate painted surfaces to rougher metal or stone.
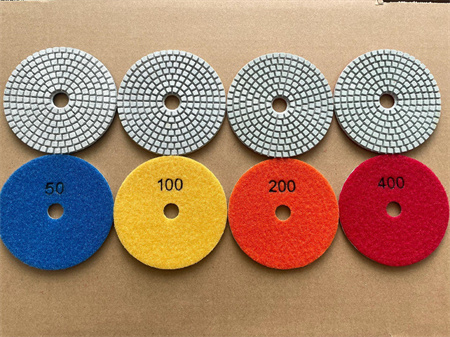
For professionals, time is money, and the use of advanced polishing pads allows for faster turnaround without compromising quality. This is particularly important in industries where deadlines are tight, and productivity is key. Whether in an auto body shop, a woodworking facility, or a metalworking plant, the ability to complete polishing tasks more efficiently allows workers to take on more projects and meet client demands with greater confidence.
The shift to advanced pads also contributes to the overall health and safety of the work environment. Traditional polishing methods often involved a lot of physical strain, as operators had to apply significant pressure to achieve the desired result. Modern pads are designed to require less force, making the polishing process not only quicker but also less physically demanding. This reduces operator fatigue and minimizes the risk of injury, contributing to a safer and more productive workday.
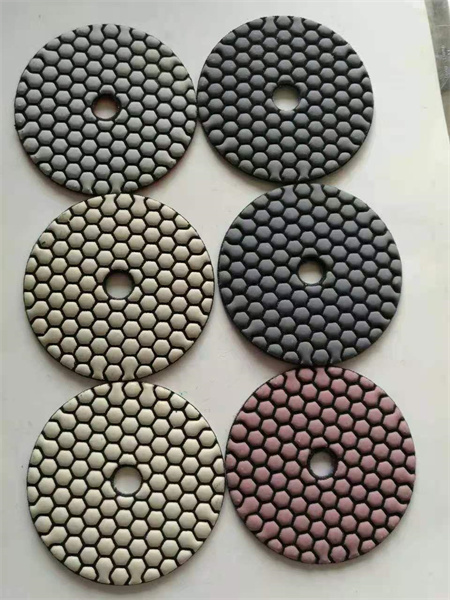
In conclusion, the adoption of advanced polishing pads is reshaping the way industries approach polishing tasks. With their ability to increase efficiency, improve quality, and enhance safety, these pads offer a compelling solution for businesses looking to stay competitive in a fast-paced world. As technology continues to evolve, we can expect even more breakthroughs in polishing pad design, making this an exciting time for professionals in every field who rely on polishing as part of their craft.