How to Minimize Energy Use in Pad Manufacturing
In today’s rapidly changing industrial landscape, sustainability has become more than just a buzzword. For manufacturers, the pressure to reduce energy consumption while maintaining product quality and profitability is stronger than ever. Pad manufacturing, a process essential to producing a variety of consumer and industrial products, is no exception. With energy costs on the rise and environmental concerns growing, businesses in this sector are increasingly looking for ways to minimize energy use without compromising efficiency or product integrity.
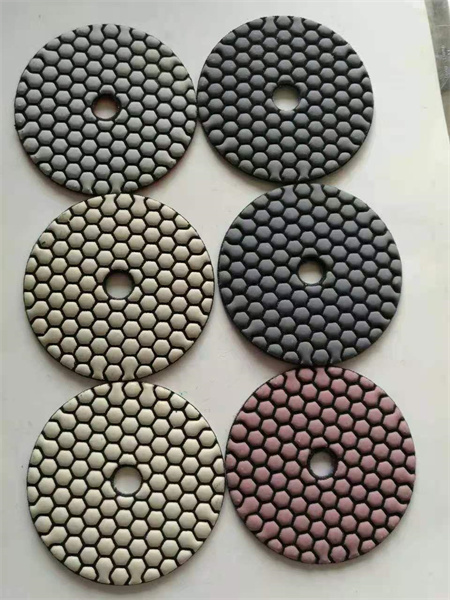
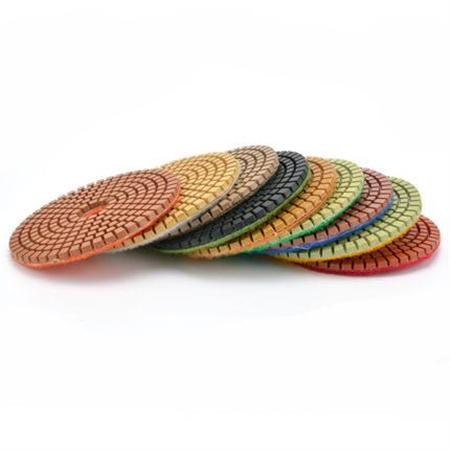
Another area that offers substantial energy savings is temperature control. Pad manufacturing often requires precise temperature regulation, whether during curing, drying, or molding processes. However, maintaining consistent temperatures can lead to excess energy use if the systems are not optimized. Upgrading insulation in key areas, fine-tuning thermostats, or using energy-efficient heating and cooling systems can drastically cut down on the energy required to keep temperatures within the desired range. Furthermore, incorporating renewable energy sources such as solar or wind power into the facility’s energy mix can offset some of the electricity used in heating or cooling processes, making the entire operation more sustainable.
Another important consideration in minimizing energy use is reducing waste during the manufacturing process. Energy is not just consumed by machines—it’s also wasted when materials are discarded or products are defective. Lean manufacturing principles, such as the 5S methodology, can help streamline operations and reduce inefficiencies. By minimizing defects and optimizing material usage, manufacturers can lower energy expenditure in both production and waste disposal.
Moreover, integrating energy management systems (EMS) can help track energy consumption in real-time and identify areas for improvement. These systems allow manufacturers to set energy goals, monitor usage patterns, and receive alerts when energy consumption spikes. Armed with this data, facilities can make informed decisions about where to implement energy-saving measures and track the success of their efforts over time. In some cases, an EMS can also help identify the best times to operate high-energy equipment, taking advantage of off-peak electricity rates and further lowering overall energy costs.
Training and educating employees also plays a pivotal role in reducing energy consumption. By fostering a culture of energy efficiency, where every worker understands the importance of minimizing energy use, the company can build a more sustainable operation. Simple actions, like turning off machines when not in use, shutting off lights in unoccupied areas, or ensuring doors and windows are sealed tightly during heating and cooling cycles, can add up to significant energy savings.
To complement internal efforts, manufacturers should also consider collaborating with suppliers who share a commitment to sustainability. By working closely with raw material suppliers and logistics partners, companies can minimize the carbon footprint of their entire supply chain. Opting for local suppliers or using more energy-efficient transport methods can help reduce the overall energy usage associated with raw material procurement and distribution.
In an industry where energy efficiency directly impacts both the bottom line and environmental footprint, it’s clear that minimizing energy use in pad manufacturing is not only the right thing to do—it’s also a smart business decision. Through equipment upgrades, process optimization, waste reduction, and energy monitoring, manufacturers can drastically reduce their energy consumption. Moreover, when combined with employee education and supplier collaboration, these strategies create a comprehensive approach to sustainability that benefits both the business and the planet. In the long run, energy efficiency is not just about cutting costs; it’s about staying competitive and preparing for a future where energy resources are more precious than ever.
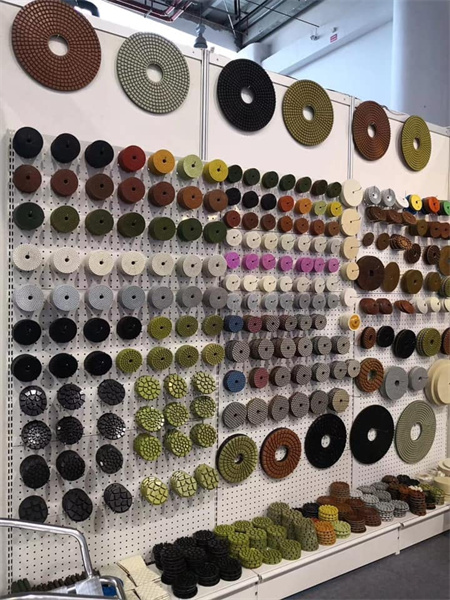