Emerging Trends in Abrasive Tools Manufacturing
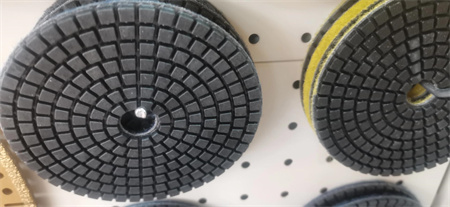
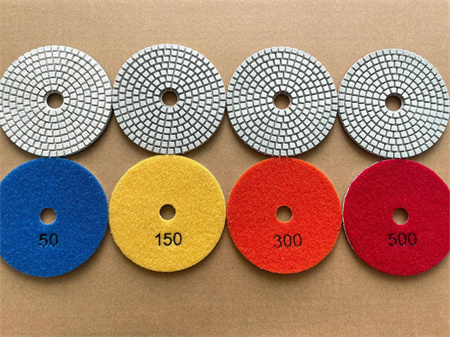
The rise of automation is another significant trend in abrasive tools manufacturing. Automated systems are revolutionizing the production process, allowing manufacturers to achieve greater consistency and precision in tool creation. By incorporating robotics, machine learning, and artificial intelligence, manufacturers can optimize the design and production of abrasive tools with minimal human intervention. This not only speeds up the production timeline but also reduces human error, ensuring higher-quality end products. The result is an overall increase in manufacturing efficiency, which is crucial in meeting the ever-growing global demand for advanced abrasive solutions.
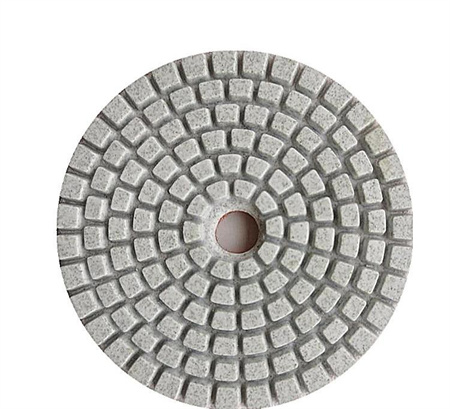
Sustainability is another driving force in the abrasive tools industry. With growing concerns about environmental impact, manufacturers are adopting eco-friendly practices that reduce waste and energy consumption. This includes developing abrasives that are more efficient, use less energy during the manufacturing process, and are made from recycled or sustainable materials. Additionally, there is a push for the development of “green” abrasives—tools that reduce harmful emissions during their use and disposal. Sustainability is becoming a competitive advantage, as industries increasingly prioritize green solutions that align with their environmental goals.
The advent of digital technologies is also making waves in abrasive tools manufacturing. The use of sensors, real-time data analytics, and the Internet of Things (IoT) is improving how manufacturers monitor and control the quality of their products. With real-time feedback on wear patterns, temperature changes, and tool performance, manufacturers can adjust their production processes instantly, ensuring better quality control and reducing the chances of defects. This digital revolution also paves the way for predictive maintenance, where tools are monitored for signs of wear and replaced before they fail, reducing downtime and increasing overall productivity.
Moreover, the demand for abrasives in emerging industries is driving innovation. For example, the rise of electric vehicles (EVs) has led to a need for abrasives that can handle the precision cutting and grinding required for battery manufacturing. Similarly, the aerospace industry is pushing the limits of abrasive technology to meet the demands of complex, high-tolerance parts. As industries like EVs, 3D printing, and robotics evolve, they bring new challenges that require specialized abrasives that can deliver optimal results in increasingly complex applications.
The ultimate takeaway from these trends is that abrasive tools manufacturing is not just about traditional grinding and cutting anymore—it’s a dynamic field that embraces technology, customization, sustainability, and industry-specific innovation. With advanced materials, automation, and a focus on green production practices, the future of abrasive tools looks brighter than ever. Manufacturers who embrace these emerging trends will be better positioned to meet the demands of an ever-changing industrial landscape and continue to push the limits of what’s possible. As these trends continue to develop, the ultimate goal is clear: to deliver cutting-edge abrasive tools that offer unmatched performance, precision, and sustainability for a wide range of industries.