Evaluating Manufacturer Certifications Before Ordering
When it comes to purchasing products, whether for personal use, resale, or industrial purposes, one of the most crucial factors to consider is the certification status of the manufacturer. Certifications are more than just logos on a product or website – they represent a standard of quality, safety, and reliability. Before committing to an order, evaluating a manufacturer’s certifications can make all the difference in ensuring you receive the best value for your investment.
Understanding the significance of these certifications can help you avoid costly mistakes, reduce the risk of purchasing substandard goods, and guarantee that the products meet the necessary safety regulations. But how do you go about evaluating a manufacturer’s certifications to ensure they align with your needs?
First, consider the specific industry standards relevant to your purchase. For instance, if you’re buying electronics, look for certifications like CE (Conformité Européene), UL (Underwriters Laboratories), or RoHS (Restriction of Hazardous Substances). These certifications indicate that the products meet required safety and environmental standards. For industrial machinery, certifications such as ISO 9001 or ISO 14001 might be more applicable, showcasing the manufacturer’s commitment to quality management systems and environmental responsibility.
To start the evaluation process, take a close look at the certificates themselves. Do they appear legitimate, or do they look generic or outdated? Fake or expired certifications can sometimes be disguised as legitimate, and a superficial glance might not reveal their true nature. A reputable manufacturer will provide verifiable documentation that you can trace back to the certifying body. If a manufacturer is hesitant to share their certifications or provides documents that seem incomplete or unclear, consider this a red flag. Transparency is a key indicator of a trustworthy partner.
Next, consider the reputation of the certifying organization. Well-established certifying bodies like the International Organization for Standardization (ISO), the American National Standards Institute (ANSI), or the Global Organic Textile Standard (GOTS) have strict, clearly defined criteria for certification. These organizations are globally recognized for maintaining high standards and ensuring that their certifications are not easily awarded without thorough vetting. If the certifications are from lesser-known or obscure organizations, you should take extra steps to verify their legitimacy.
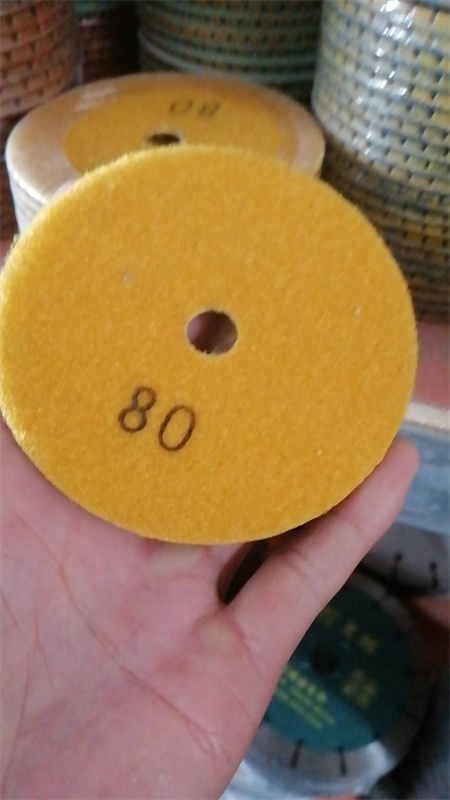
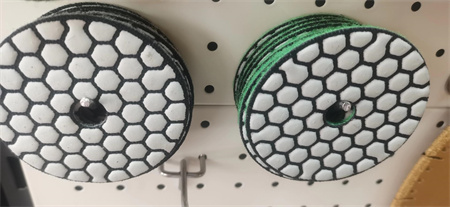
Don’t underestimate the importance of checking the geographical relevance of the certifications. Depending on where you intend to sell or use the product, certain certifications might be more valuable or necessary than others. For example, a product certified for the European Union market may not automatically meet the requirements for the U.S. market. Similarly, some certifications are region-specific, like the FSC (Forest Stewardship Council) certification for sustainable forestry practices, which may be more important in certain countries due to environmental regulations.
Beyond the certifications themselves, consider the manufacturer’s track record. Are there any customer reviews or testimonials about the manufacturer’s products? Are there complaints about poor quality or safety issues that have come to light after certification was awarded? A manufacturer can hold the right certifications but still fall short in delivering high-quality products consistently. Check for any past product recalls or safety violations, as these can indicate deeper issues with manufacturing practices despite their certified status.
One last consideration when evaluating manufacturer certifications is their commitment to innovation and staying ahead of industry trends. A manufacturer that continually seeks new certifications to stay on the cutting edge of technology, sustainability, and safety is likely a better partner in the long run. Manufacturers who invest in research and development (R&D) and stay current with changing regulations tend to produce products that are not only safe and reliable but also aligned with market demands.
In summary, evaluating manufacturer certifications before placing an order involves a comprehensive process of verifying the legitimacy, scope, and relevance of certifications, understanding the manufacturer’s reputation, and ensuring the certifications are up-to-date. Taking these steps will not only protect your business from potential risks but also ensure that you are investing in high-quality, reliable products that meet both regulatory standards and customer expectations. So, next time you’re preparing to place an order, take the time to carefully evaluate those certifications – it could be the difference between success and a costly setback.
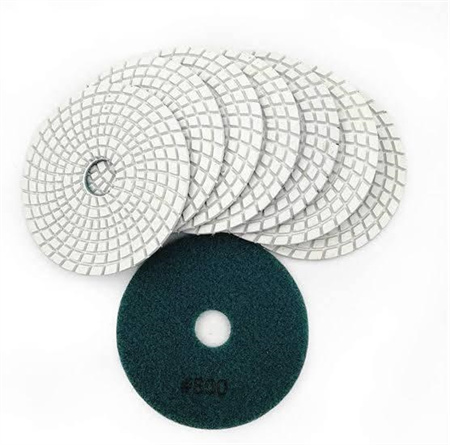