Exploring the Abrasive Properties of Diamond in Stone Polishing
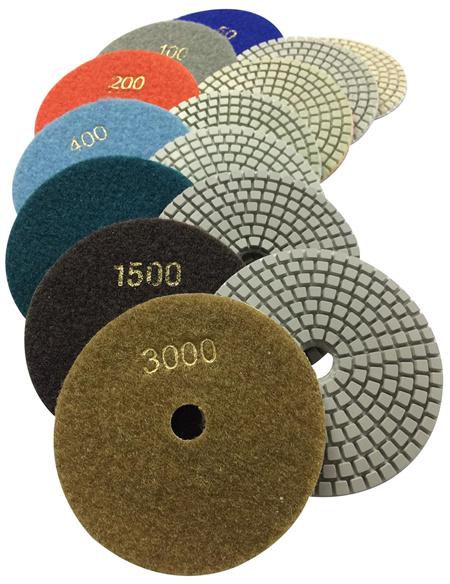
Diamonds are celebrated for their extraordinary hardness, a feature that is central to their role in abrasive applications. On the Mohs scale of mineral hardness, which ranks minerals from 1 to 10, diamond stands at a perfect 10—harder than any other naturally occurring material. This remarkable hardness allows diamonds to effectively grind and polish even the most challenging materials, including granite, marble, and other tough stones that might resist other abrasives.
The hardness of diamond doesn’t just make it effective in cutting through tough materials; it also ensures a finer, smoother finish. When diamonds are used in stone polishing, they don’t merely scratch or dull the stone’s surface; instead, they create a mirror-like sheen by removing the tiniest imperfections and micro-level scratches. This precision is unmatched by other abrasives, ensuring that the polished stone retains its natural luster and beauty. Whether polishing a gemstone or refining a piece of architectural stonework, diamond abrasives are capable of achieving a level of perfection that other materials can only dream of.
Diamond abrasives come in many forms—powder, grit, and diamond-coated tools are common in the stone polishing industry. Each form is designed to optimize the polishing process depending on the stone’s hardness and the desired finish. Diamond dust or powder is often used for fine polishing tasks, where a smooth, high-gloss surface is required. Coarser diamond grits, on the other hand, are more suitable for heavy grinding and initial stages of the polishing process. The versatility of diamond abrasives allows craftsmen to select the right type for the job, making it a valuable asset for both small-scale artisans and large-scale manufacturing operations alike.
Beyond their hardness, diamonds have another key feature that makes them ideal for polishing: their ability to stay sharp. Many other abrasives, such as silicon carbide or aluminum oxide, tend to wear down quickly as they are used, losing their effectiveness over time. In contrast, diamond particles maintain their sharp edges much longer, allowing them to sustain their cutting power and provide consistent results throughout the polishing process. This durability is especially beneficial in industrial settings, where time and efficiency are crucial, and it also ensures that polishing jobs are completed with minimal interruption or need for replacement materials.
What also makes diamonds so effective in stone polishing is the way they interact with the stone’s surface. As the diamond abrasives grind against the stone, they break down into smaller fragments, constantly exposing new sharp edges. This continuous renewal of sharp surfaces ensures that the abrasive action remains effective, allowing for a finer and more even finish. This process, known as “self-sharpening,” is a key reason why diamond abrasives are so efficient and capable of producing such high-quality results.
The role of diamonds in stone polishing extends far beyond mere utility—they bring a touch of luxury to the process. In the world of gemstones, diamonds are often used not just for polishing, but for enhancing the stone’s natural beauty. When used properly, diamond abrasives can bring out the true brilliance and color of a gem, making it more vibrant and captivating. This is why diamond polishing is often the final step in the crafting of precious stones, where the goal is not just to shape the stone but to reveal its full potential.
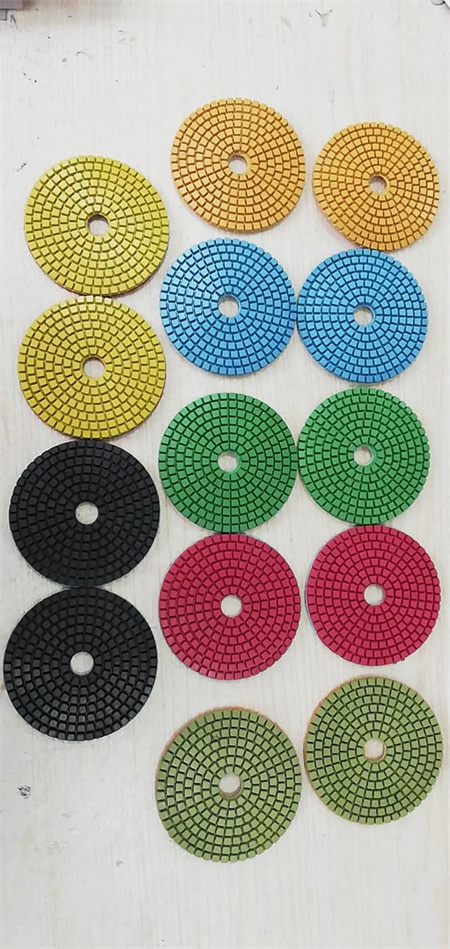
In conclusion, the abrasive properties of diamonds are what elevate stone polishing to an art form. From their unmatched hardness and durability to their ability to create a flawless, high-gloss finish, diamonds provide the precision and quality that other abrasives simply cannot match. Whether used to polish gemstones, architectural stones, or a range of other materials, diamond abrasives continue to set the standard for excellence, ensuring that every polished surface shines with unmatched clarity and brilliance.
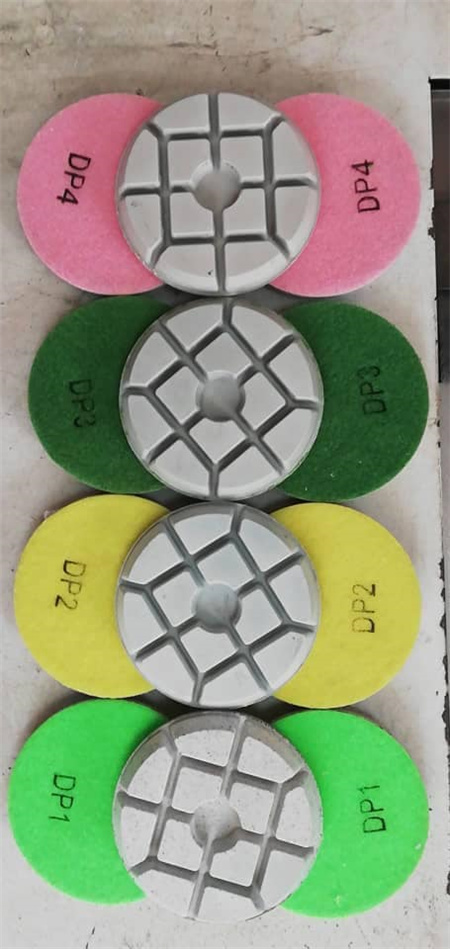