How a Supplier Helped a Client Scale Their Stone Polishing Business
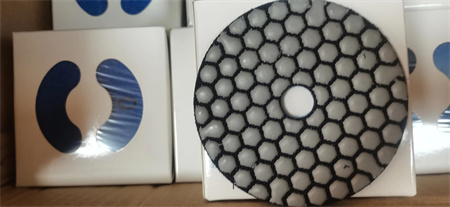
When the client first came to their supplier, they were facing challenges that many small businesses in niche industries encounter: limited resources, a growing demand for their services, and an inability to keep up with production demands. The client had built a reputation for high-quality stone polishing but was struggling to expand. They had the craftsmanship, the passion, and the clients, but their operations were slow and inefficient, leading to long lead times and missed opportunities.
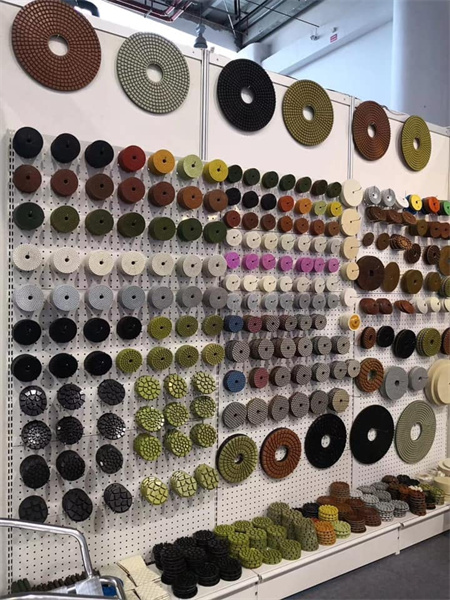
A collaborative approach quickly took shape. Instead of just selling off-the-shelf products, the supplier started by conducting a thorough review of the client’s existing setup. This included an analysis of their polishing machinery, the types of abrasives they were using, and the overall workflow in their workshop. The goal wasn’t to just make a sale but to provide a holistic solution that would streamline operations and improve productivity.
The first step was upgrading the client’s polishing machines. The supplier introduced high-performance, durable polishing machines designed for heavy-duty use, capable of processing large quantities of stones with a smoother finish in less time. These machines didn’t just improve the quality of the final product—they drastically reduced the time it took to complete each job. For a business that depended on efficiency and speed, this was a game changer.
Next came the selection of the right abrasives. The supplier took the time to understand the specific types of stones the client worked with most often, from marble to granite, and recommended a tailored range of abrasives. Each abrasive was chosen to maximize both speed and finish quality, reducing the need for multiple passes and significantly lowering material waste. This choice of abrasives not only improved the quality of the polish but also allowed the client to take on a wider range of projects, including more high-end, demanding clients.
Perhaps the most important contribution the supplier made was providing ongoing technical support and training. The stone polishing business didn’t just need new equipment—it needed to know how to get the most out of it. The supplier’s team conducted hands-on training sessions with the client’s staff, helping them understand the ins and outs of the new machines, the proper use of abrasives, and best practices for efficient workflow. This wasn’t just a one-time transaction; it was the beginning of a long-term partnership. As the supplier and client continued to work together, the business began to refine its processes further, improving both output and quality.
As production capacity increased, the stone polishing business found itself able to handle larger orders, faster turnarounds, and a greater variety of projects. The client soon noticed a significant boost in their bottom line. With more efficient machinery, better materials, and a more knowledgeable team, the business could scale without compromising on quality. Word spread, and new clients came on board, attracted by the speed, precision, and superior finish of the polished stone products.
But the supplier didn’t stop there. They continued to provide regular updates on the latest trends in stone polishing technology, ensuring the client’s operations stayed ahead of the curve. When new innovations in polishing materials and equipment emerged, the supplier was quick to share these developments, helping the business maintain its competitive edge.
Today, the stone polishing business stands as a prime example of how the right supplier partnership can transform a small operation into a scalable, successful enterprise. By offering not only high-quality products but also expert advice, technical support, and a tailored approach to the client’s unique challenges, the supplier played an instrumental role in the business’s growth.
For businesses in niche industries like stone polishing, having the right partner can make all the difference. It’s about more than just selling products—it’s about creating a relationship that supports long-term success. In this case, the supplier didn’t just help the client scale their operations; they helped them realize their full potential in an ever-evolving market.
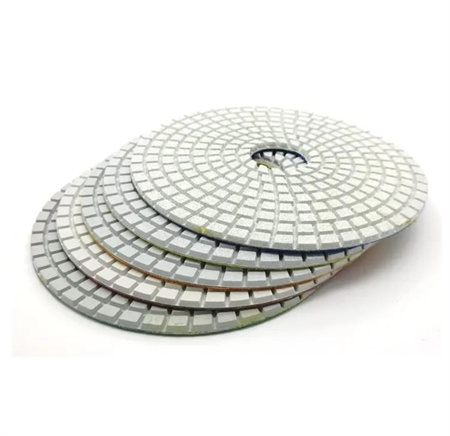