How Weather Affects Stone Polishing Performance
Stone polishing is both an art and a science. Whether it’s marble, granite, or any other natural stone, achieving the perfect shine requires careful attention to detail and, surprisingly, the weather. The impact of environmental conditions on the polishing process can be profound, influencing everything from the quality of the finish to the efficiency of the polishing work. Understanding how weather affects stone polishing performance is crucial for achieving consistent, high-quality results.
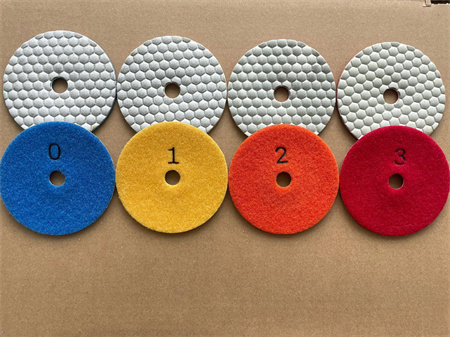
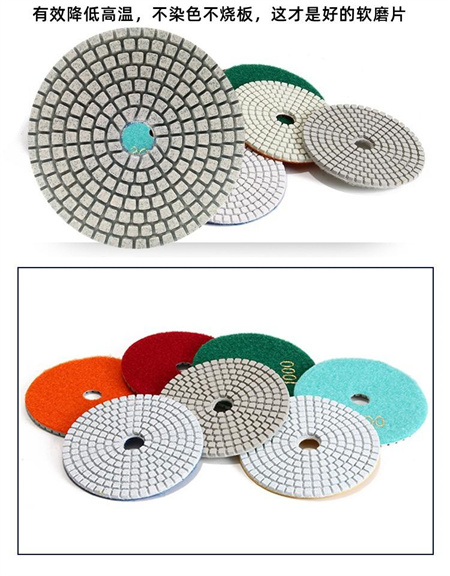
Wind speed and airflow can also influence stone polishing. A breezy day may seem like a blessing when working outside, but strong winds can carry dust and debris that end up sticking to the wet stone surface. This contamination can mar the finish and prolong the polishing process. Conversely, a lack of airflow can cause moisture to linger on the stone’s surface, slowing down the curing of the polishing agents. Ideally, a slight breeze is perfect for stone polishing, as it helps with the evaporation process without blowing particles onto the surface.
The time of year can also impact the performance of stone polishing. During the summer, higher temperatures and greater humidity can cause more challenges, as discussed earlier. Conversely, winter may bring more predictable conditions, but colder temperatures can make working outside uncomfortable and more difficult. However, with the right equipment and planning, winter polishing can yield excellent results, provided precautions are taken to avoid freezing of materials or any potential surface damage caused by low temperatures.
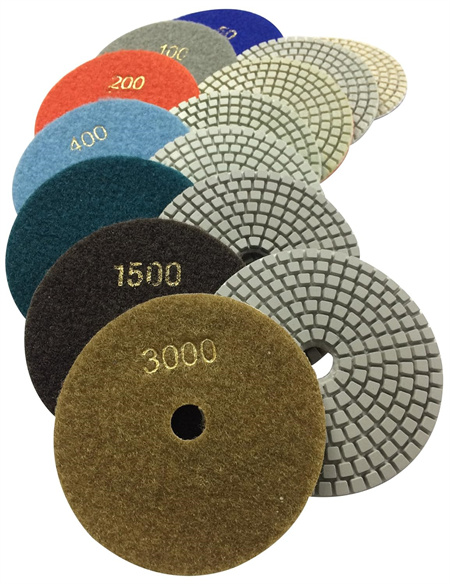
Stone characteristics can also influence how weather affects polishing performance. Softer stones, such as limestone, tend to be more sensitive to temperature and humidity changes, while harder stones like granite are less affected. However, all stones can suffer from poor environmental conditions during the polishing process. It’s essential to understand the specific needs of the stone you’re working with to adjust your approach accordingly.
Proper planning is key to navigating the challenges posed by weather when polishing stone. If you’re working outside, it’s essential to monitor the forecast closely. If you’re aware of impending rain or an unusually humid day, it might be worth rescheduling the polishing work. Some professionals may choose to invest in portable shelters or tarps to protect stone surfaces from the elements. Others may opt for indoor facilities where temperature and humidity levels can be controlled more effectively, ensuring the polishing process is not compromised.
In summary, while weather might seem like an uncontrollable factor, it plays a significant role in the performance and outcome of stone polishing. From temperature and humidity to wind and rain, each aspect of the weather can affect the materials, tools, and techniques used in the polishing process. By understanding these influences and adjusting accordingly, stoneworkers can ensure the best possible results, regardless of the conditions outside.