Emerging Technologies in Resin Bonding for Pads
The world of resin bonding for pads is evolving at a rapid pace, driven by advancements in materials science, precision engineering, and manufacturing techniques. As industries continue to demand higher performance, durability, and cost-effectiveness from their products, resin bonding is becoming an increasingly critical process in a variety of applications—from automotive and electronics to medical devices and consumer goods. In this dynamic landscape, emerging technologies are reshaping the way we approach resin bonding, offering new possibilities and pushing the boundaries of what’s achievable.
One of the most exciting developments in this area is the advent of ultra-high-performance resins that offer superior bonding strength, heat resistance, and durability. These new resins are engineered to withstand extreme environmental conditions, making them ideal for applications where traditional bonding materials fall short. With advancements in polymer chemistry, manufacturers can now produce resins that are not only stronger but also more adaptable to different surfaces and materials. This versatility opens up a whole new range of applications, from automotive brake pads that must endure high temperatures and friction to advanced medical devices requiring precise and secure bonding.
Another significant breakthrough is the integration of nanotechnology into resin bonding. By incorporating nanoparticles into the resin matrix, manufacturers can enhance the mechanical properties of the bond without sacrificing flexibility or toughness. Nanoparticles, such as carbon nanotubes or silica, improve the resin’s resistance to wear, fatigue, and thermal degradation, resulting in longer-lasting bonds. This technology is particularly relevant in industries where high-performance pads are essential, such as in aerospace, defense, and industrial machinery. Nanotechnology also allows for more precise control over the resin’s curing process, which ensures a more uniform and consistent bond every time.
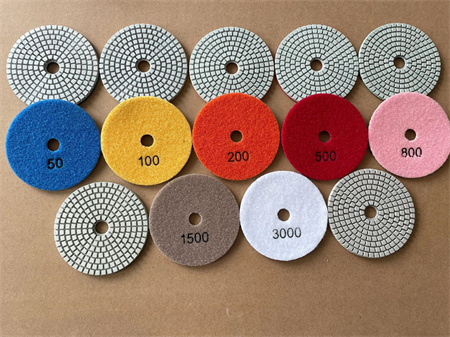
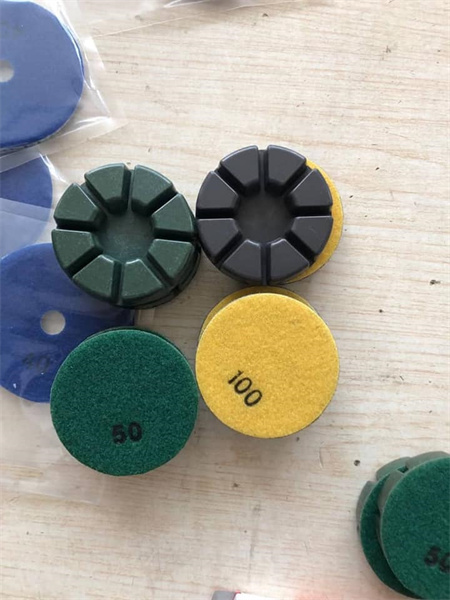
Moreover, automation in resin bonding is streamlining production lines, reducing labor costs, and increasing throughput. Robots equipped with advanced vision systems are now able to apply resin to pads with a level of precision that was previously impossible. These automated systems not only improve the consistency of the bonding process but also increase the speed at which products can be produced. For industries with high-volume manufacturing, such as automotive and electronics, this means significant savings in time and money.
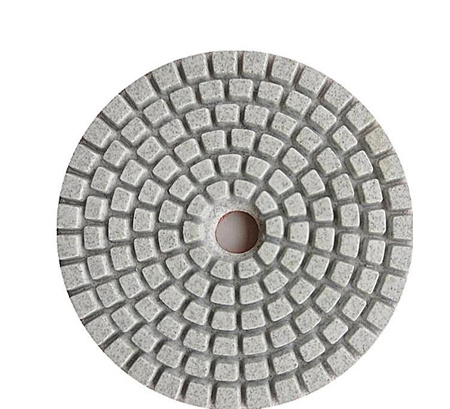
The potential of emerging technologies in resin bonding for pads is immense. As material science, automation, and sustainability continue to evolve, the future of resin bonding looks brighter than ever. With faster curing times, stronger bonds, and more environmentally friendly processes, these innovations are enabling industries to create better, more reliable products. From enhancing the performance of everyday items to ensuring the safety and reliability of critical components, emerging technologies in resin bonding are not just shaping the future—they’re helping to build it.